Harnessing the Power of Digital Twins: Revolutionizing Industries
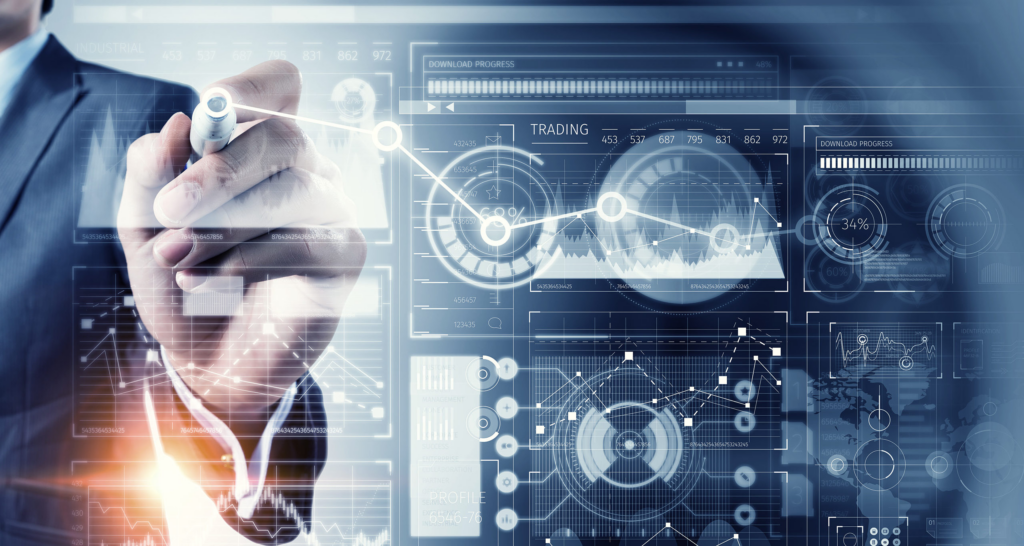
Transforming Business Operations with Digital Twins: A Path to the Future
In a world where industries are constantly evolving to meet the demands of the digital age, the concept of digital twins has emerged as a game-changer. These virtual models, which mirror real-world entities and processes, have found applications across various sectors, such as manufacturing, energy, telecommunications, agriculture, and retail. While the roots of digital twins can be traced back to NASA’s Apollo missions in the 1960s and product lifecycle management in manufacturing during the 1980s, it’s the recent advancements in software technologies that have accelerated their development and widespread adoption.
The driving force behind the adoption of digital twins is the opportunity for businesses to leverage technology to address their unique challenges. However, capitalizing on the benefits of digital twins and integrating them seamlessly into all aspects of business operations requires a well-defined strategy. Furthermore, establishing a robust technological foundation is essential, with technologies like artificial intelligence (AI), machine learning (ML), internet of things (IoT), cloud computing, and automation forming the core components of digital twin systems.
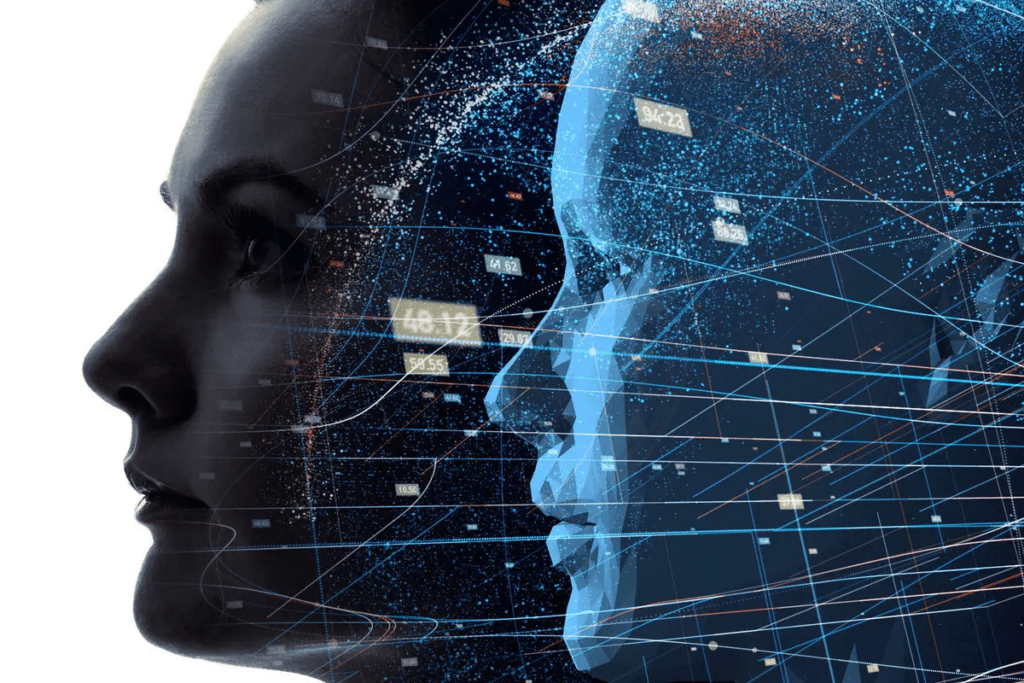
In addition to the mentioned aspects (AI, IoT..), the most essential technological foundation for a working Digital Twin is a working model/equation. In order to set up such a model/equation it requires a lot of testing of the model and all its components, as well as experts who know how different conditions can influence components of the equation. Currently the data collection and testing frequently takes more time, then e.g. the product lifetime of an e-car. However, the more data there will be gathered, the easier it will be in the future to create reliable Digital Twins.
Challenges of Implementing Digital Twins in the Automotive Industry
The automotive industry has been at the forefront of adopting digital twin technology to enhance the design, production, and operation of vehicles. While the potential benefits are significant, there are several challenges that automotive manufacturers and stakeholders face when implementing digital twins in this highly dynamic and complex sector. This chapter explores these challenges and potential solutions.
Data Integration and Quality:
One of the fundamental challenges is the integration of data from various sources and ensuring data quality. In the automotive industry, data comes from sensors, IoT devices, CAD systems, and more. Ensuring that all this data is integrated seamlessly into the digital twin model while maintaining its accuracy and consistency is a complex task.
Solution: Implementing robust data governance and quality control processes, as well as using standardized data formats and protocols, can help address this challenge. Additionally, employing advanced analytics and artificial intelligence (AI) to clean and preprocess data can enhance data quality.
Scalability:
Creating digital twins for individual vehicle components is relatively straightforward, but when scaling up to model entire vehicles or even entire manufacturing plants, complexity grows exponentially. Ensuring that digital twin models remain manageable and efficient as they scale is a significant challenge.
Solution: Developing hierarchical digital twin models that allow for zooming in on specific components or subsystems while maintaining an overview of the entire vehicle or plant can address scalability issues. Additionally, leveraging cloud computing and distributed computing resources can improve performance.
Real-Time Data Processing:
The automotive industry relies on real-time data for decision-making. Digital twins are only as valuable as the data they operate on. Managing and processing vast amounts of real-time data to provide accurate and up-to-date representations of physical assets is a challenge.
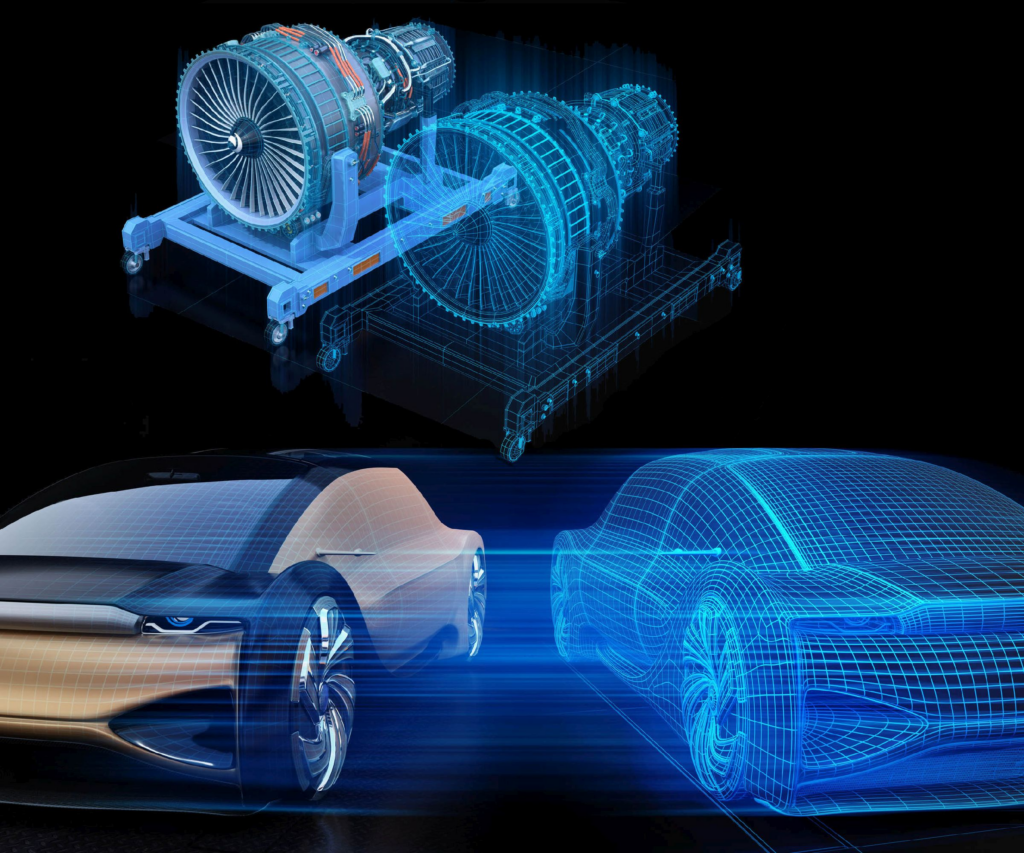
Solution: Employing edge computing and fog computing to process data closer to the data source can reduce latency and enable real-time monitoring and control. Furthermore, AI and machine learning algorithms can help identify and act upon critical data patterns swiftly.
Security and Privacy:
The automotive industry is particularly concerned with the security and privacy of the data involved. Ensuring that sensitive information related to vehicle designs, prototypes, and customer data is adequately protected is crucial.
Solution: Implementing robust cybersecurity measures, encryption, and access control mechanisms can safeguard digital twin data. Compliance with industry standards and regulations, such as GDPR for data privacy, is essential.
Interoperability
The automotive industry relies on a multitude of software applications and systems. Ensuring that digital twins can seamlessly integrate with existing tools and platforms can be a considerable challenge.
Solution: Embracing open standards for data exchange and application programming interfaces (APIs) can facilitate interoperability. Establishing partnerships and collaborations with software vendors to develop integrated solutions is another approach.
Cost and Resource Constraints:
Creating and maintaining digital twins requires significant financial and human resources. Small and mid-sized automotive companies may face challenges in terms of the initial investment and ongoing operational costs.
Solution: Tailoring digital twin implementations to the specific needs and resources of each company can help mitigate this challenge. Consideration of cloud-based solutions or outsourcing aspects of digital twin development and management may also be cost-effective.
Change Management:
Integrating digital twin technology often requires significant changes in organizational culture, processes, and skills. Resistance to change and a lack of understanding of the technology can hinder successful implementation.
Solution: Investing in employee training and change management programs can help employees adapt to new technologies and embrace digital twin concepts. Leadership should also champion the adoption of digital twins to foster a culture of innovation.
Navigating the World of Digital Twins
Digital twins can significantly enhance decision-making and facilitate effective actions in various industries and applications. Here’s how they can help:
Accurate Simulation:
Digital twins provide a highly accurate, real-time simulation of physical objects or processes. This simulation allows organizations to experiment with different scenarios, test hypotheses, and predict outcomes. By having a virtual replica of the physical world, decision-makers can make informed choices without the need for costly physical prototypes or experiments.
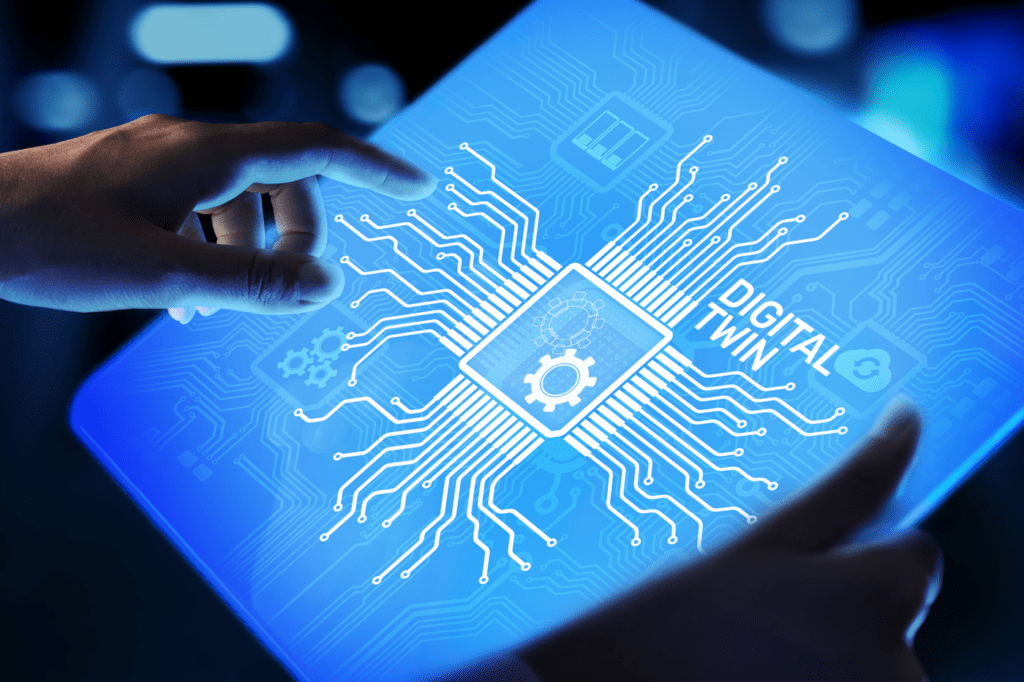
Data-Driven Insights:
Digital twins continuously collect data from sensors and various sources in real-time. This data is processed and analyzed to provide actionable insights. Decision-makers can use these insights to understand the current state of the physical system, identify trends, and make data-driven decisions. For example, in manufacturing, digital twins can predict when a machine might fail and trigger maintenance preemptively, reducing downtime.
Remote Monitoring:
Digital twins enable remote monitoring and control of physical assets or processes. This is especially valuable for industries with distributed operations or in situations where on-site monitoring is challenging. Decision-makers can remotely assess the condition of assets, adjust parameters, and take actions as needed.
Optimization:
Digital twins can be used to optimize various processes. For instance, in urban planning, a digital twin of a city can be employed to optimize traffic flow, energy consumption, and emergency response. By simulating different scenarios and their outcomes, decision-makers can choose the most efficient and cost-effective solutions.
Risk Mitigation:
Digital twins allow for the identification of potential risks and vulnerabilities. For example, in infrastructure management, a digital twin of a bridge can detect structural issues early on, enabling proactive maintenance to prevent accidents. Decision-makers can act to mitigate risks before they escalate.
Collaboration:
Digital twins facilitate collaboration and knowledge-sharing among teams, even if they are geographically dispersed. This collaborative environment ensures that decision-makers have access to the most up-to-date information, and they can work together to make informed decisions.
Predictive Maintenance:
In industries like manufacturing and healthcare, digital twins can predict when equipment or devices might fail. This predictive maintenance capability enables decision-makers to schedule maintenance at the optimal time, reducing downtime and costs.
Environmental Impact Assessment:
Digital twins can be used to simulate the environmental impact of various projects, such as construction, energy production, or transportation. This helps decision-makers assess the sustainability of their actions and make environmentally responsible choices.
Additionally, digital twins enable businesses to engage customers more effectively, foster cross-team collaboration using virtual 3D assets, and create self-optimized autonomous systems.
For nearly two decades, organizations have sought to digitize their assets to enhance performance and reduce defects. However, the technical infrastructure required for this, including sensors, connectivity, computing power, and storage capacity, was often beyond reach. As IT advancements have made these elements more accessible, digital twins have proliferated across industries. Recent studies indicate that a significant majority of executives are either running or planning to implement digital twins programs in their organizations.
The Impact of Digital Twins on Various Industries
Digital twins offer a multitude of practical applications that significantly impact various facets of business operations. These applications include monitoring, analyzing, predicting, prescribing, and adapting. Each of these applications plays a vital role in the success of a digital twin, with the choice of the application depending on the specific goals and needs of the organization.
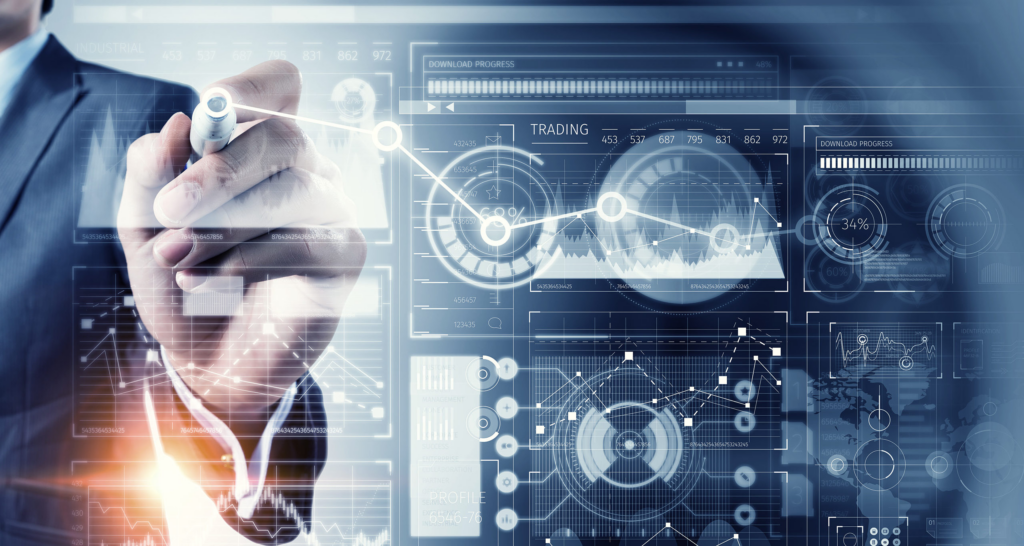
Automotive manufacturers can also use digital twin technology for performance monitoring. Digital twins offer in-depth insights into every aspect of production and maintenance.
Digital twins collect and analyze data continuously from various sensors on the vehicle. This capability allows them to monitor parameters such as manufacturing and fuel efficiency, durability, and more. Consequently, they can detect any discrepancies or issues early and address them promptly.
Tesla is an excellent example in this context. They incorporate an array of sensors within their cars to create a digital twin, enabling them to oversee the performance of the vehicles. They can keep an eye on battery health, energy consumption, and other critical factors. With this information, Tesla assists their customers in maintenance and enhances vehicle performance.
Additive manufacturing is another area where digital twins can enhance process efficiency. For instance, a digital twin of a 3D printer can simulate the printing process and identify defects. Furthermore, digital twin ecosystems can integrate various sensors and IoT devices to help manufacturers monitor processes in real-time, identify anomalies, and improve efficiency.
Real-World Applications of Digital Twins
Real-world use cases of digital twins indicate their significance in the digital transformation journey of organizations. Many view them as a strategic element in their transformation strategies, with the number of new physical assets and processes modeled as digital twins expected to increase substantially in the coming years.
Manufacturing is one of the industries that have readily adopted digital twins, using them in various ways, such as in the design and monitoring of electric motors. By creating digital twins of assets like electric motors, organizations can predict failures and enhance overall equipment effectiveness through predictive maintenance.
ANSYS is at the forefront of digital twin technology development in the construction industry. By carefully assessing the progress of their virtual twins, organizations can make accurate predictions about the performance of future products using ANSYS’ physics-based simulation combined with analytics. ANSYS collaborates with various sectors, including automotive, aerospace, military, construction, energy, and healthcare, making up their portfolio. The wide range of applications enables them to provide market solutions tailored to the specific needs of individual companies or sectors. The ANSYS Store offers both paid and free applications.
Supply chain management is another area where digital twins prove invaluable. The COVID-19 pandemic exposed vulnerabilities in supply chains, making digital twins a critical tool for optimization and resilience. These digital representations of supply chains offer real-time visibility, forecast dynamics, and support “what-if” analysis, enabling businesses to make informed decisions.
The Ecosystem of Talent and Experience
To successfully navigate the world of digital twins, organizations need trusted consulting and technology partners with domain expertise. These partners should implement battle-tested technology, frameworks, and accelerators while leveraging advanced technologies like AI, ML, IoT, cloud, and automation to solve complex business problems.
Conclusion: Embracing the Digital Twin Revolution
In conclusion, digital twins have become a transformative force in various industries. As technology advances and the digital twins space matures, organizations need to be proactive in adopting these innovative solutions. While the journey to create digital twins of all assets may be lengthy, it’s essential to keep the long-term benefits in mind. Collaboration with trusted partners is crucial to uncovering solutions and ensuring the success of digital twin initiatives.
No matter where your organization stands on its digital twin journey, investing with confidence and staying updated with the latest developments is essential. The future of business operations is intertwined with the evolution of digital twins, making it a key player in the digital transformation landscape.
If you are interested in the implementation of Digital Twin concepts for your business, please schedule a Free Consultation Call with our experts. Our experienced and reliable engineers are happy to help you with that!
Responses