The Future of Engineering in Facts and Figures as of Q3 2024.
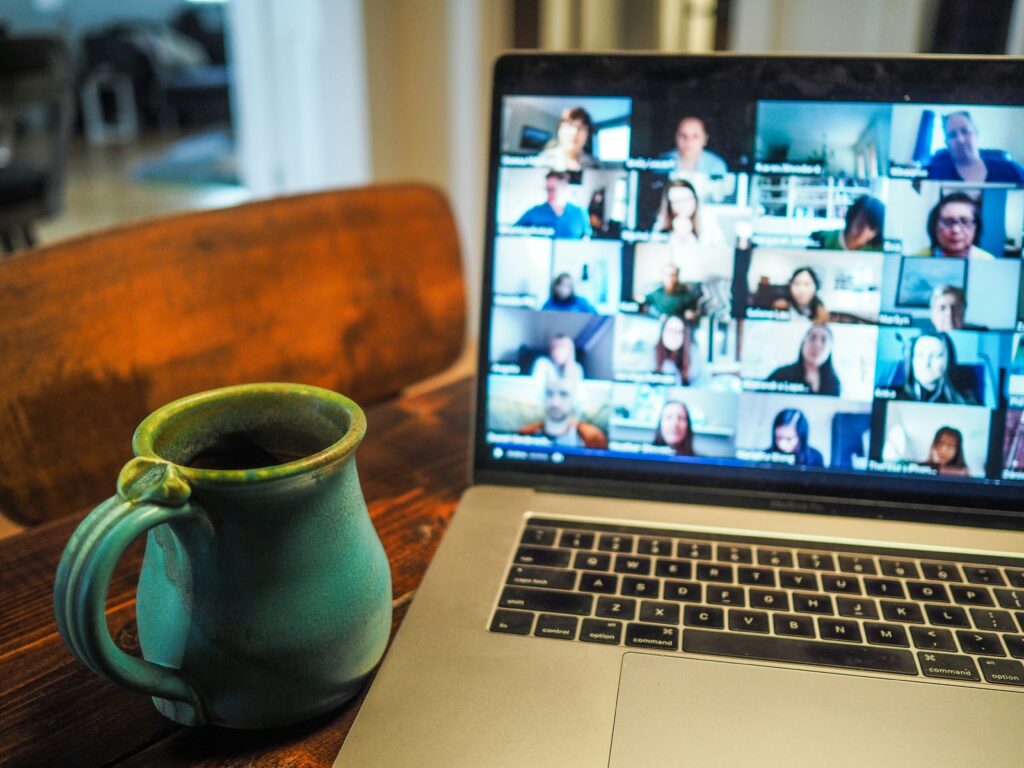
As the world around us is changing rapidly and so will the engineering sector. The future of engineering is heavily driven by chronic resource shortages, high employee turnover, and an increasing demand for remote work flexibility. As traditional engineering firms grapple with these challenges, a paradigm shift is inevitable, reshaping the way businesses operate and engage with their workforce.
In the following we will have a close look at the facts and figures, that are driving these trends.
The Resource Crunch
A study by the U.S. Bureau of Labor Statistics revealed that engineering jobs are expected to grow faster than the average of all occupations from 2023 to 2033, which translates into approximately 195,000 new jobs in the field. However, the supply of qualified engineers is struggling to keep pace.
According to a report from McKinsey & Company, 87% of organizations worldwide are either experiencing skill shortages or expect to in the coming years. This disparity poses an urgent challenge for engineering firms, compelling them to rethink recruitment and retention strategies.
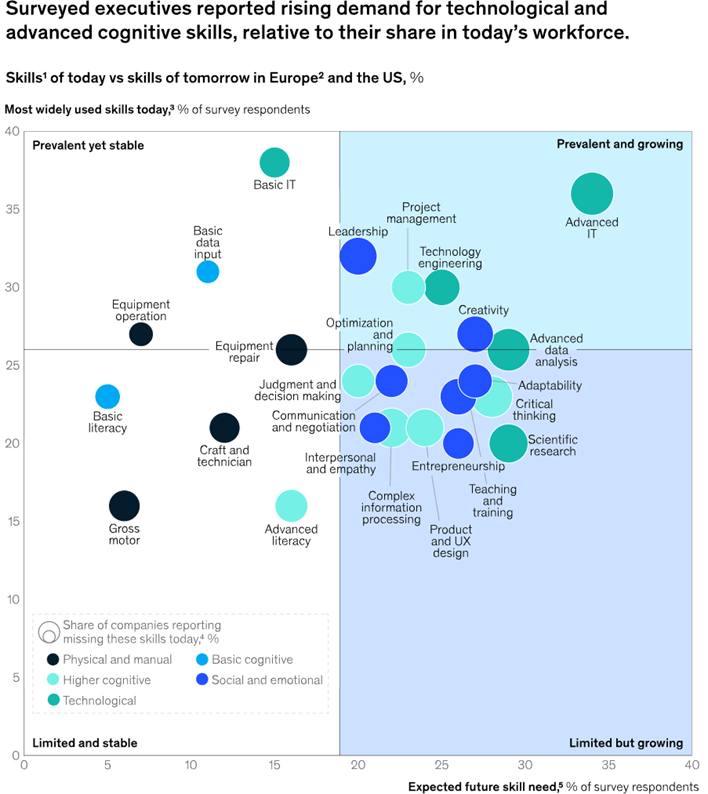
High Employee Turnover
The engineering sector has long been plagued by high turnover rates. A study conducted by LinkedIn indicates that employees in engineering roles have an above-average turnover rate with 11.5%, being at the same time the most sought-after experts according to number of InMails received from Recruiters.
Recruitment Challenges
A 2022 survey by the Institution of Engineering and Technology (IET) in the UK revealed that 49% of engineering firms reported difficulty in recruiting skilled engineers. The primary challenges include a lack of experience among applicants and an engineering or technical skill gap among candidates.
The Shift to Flexibility
As remote work becomes the new standard, engineers are seeking greater flexibility in their employment arrangements. Buffer’s State of Remote Work report indicates that 98% of remote workers prefer to work remotely at least some of the time for the rest of their careers.
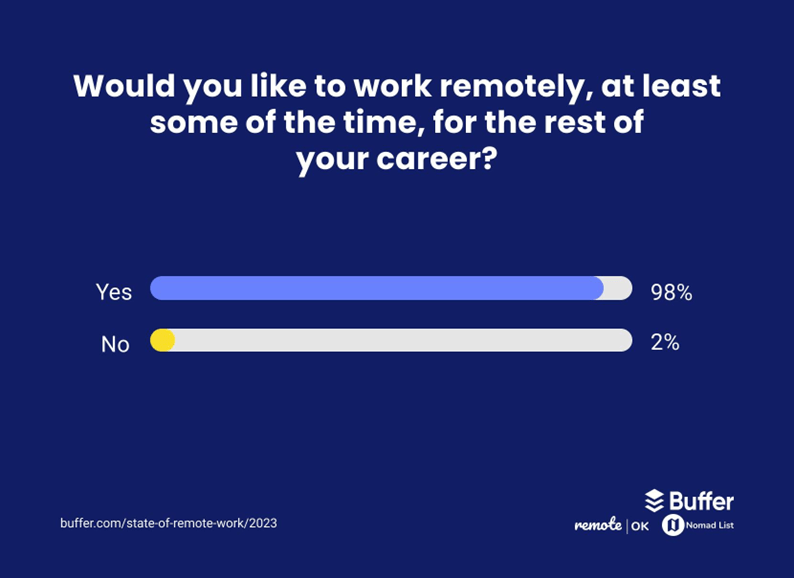
A survey conducted by McKinsey in 2022 found that 87% of employees who are provided with at least some remote work options take advantage of this opportunity, averaging three days per week working from home. Those with full-time flexible work arrangements tend to spend slightly more time remote, averaging 3.3 days each week. Notably, 12% of respondents whose employers only provide part-time or occasional remote work report that they managed to work from home five days a week. This discrepancy highlights the tension between the level of flexibility employers offer and the demands of employees.
Conclusion
In conclusion, the afore-mentioned emerging trends will lead to traditional employment stop functioning in the common way and a sudden shift towards a platform-based approach.
By adopting this approach, organizations can tap into a diverse talent pool without the limitations of traditional employment, paving the way for a future where the conventional notion of companies may evolve dramatically.
At WiredWhite, we are at the forefront of this shift, already now applying a platform-based virtual coworking space for our engineering projects. Our integrated tools like online meeting systems and project manager, allow to maximize efficiency while cooperating with engineering experts world-wide.
You are an engineering or technology expert and want to become part of the team? Then join us now.
You are a company representative seeking support in drive technologies or renewables? Please contact us here.
Responses