Advanced Modeling & Simulation of Electric Drivetrains
Modelling and simulation of electric drivetrains, electrical drives, permanent magnet synchronous machines, inverters, power converters and propulsion systems.
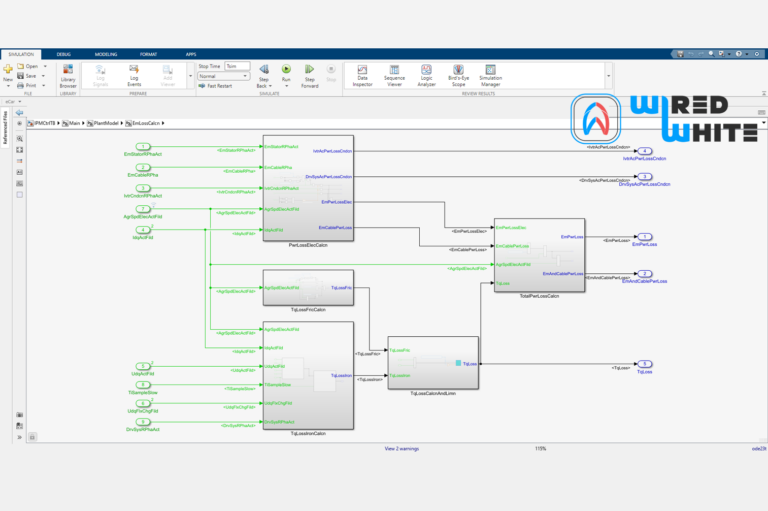
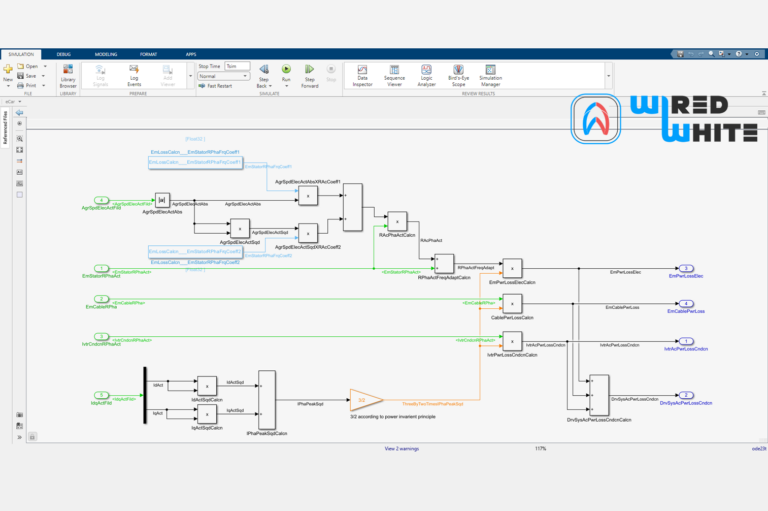
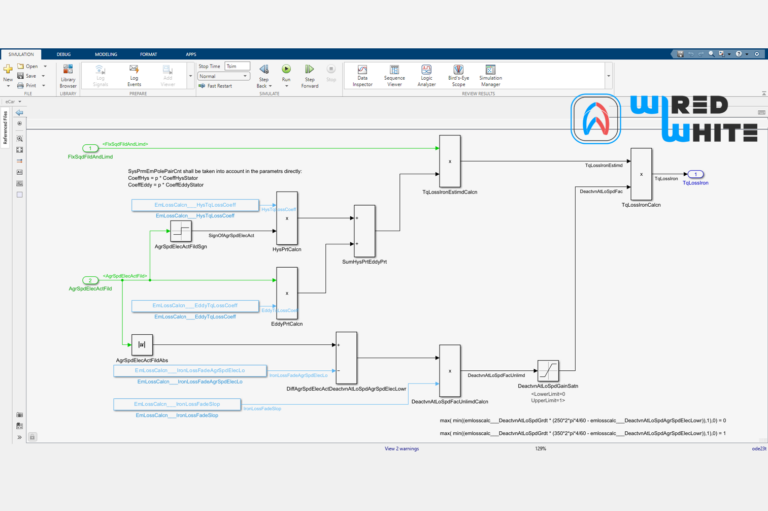
Solve Your Electric Drivetrain Modeling and Simulation Challenges:
Struggling with unclear requirements, time-consuming feasibility reviews, or supplier bottlenecks?
❌ Lack of Accurate System-Level Modeling
❌ Difficulty in Matching and Parametrizing Powertrain Components
❌ Insufficient Derating Strategies Leading to Drive Failures
❌ Inaccurate Performance and Efficiency Calculations
❌ Thermal Issues Due to Inadequate Heat Management Models
❌ High Cost and Risk Due to Incomplete Test & Validation
Accelerate your roadmap and avoid costly rework with proven engineering practices.
Comprehensive Electric Drivetrain Modeling and Simulation
🔧 Design & Feasibility
- Requirement engineering
- System modelling & design
- Software/component level requirement breakdown
- Feasibility study & review of third-party designs
- Supplier sourcing, prototype purchasing
- RFI, RFQ process organization and review
- Prototype manufacturing
- Unit tests, SW integration & validation tests
- Matching Power Converter to the electric machine
- Model parametrization
- Modelling & simulation of: synchronous machines (internal & surface mounted PMSM), Direct current (DC) motors, Asynchronous motors (ASM), Reluctance motors (SynRM), etc.
- System & drivetrain simulations
- Model-based software development
- Functional safety (FuSA)-compliant software
- Software project management
⚡ Advanced Motor Control Solutions
- Motor control algorithms: FOC / Vector control
- Torque, Speed & Power Control
- Sensorless Control Techniques
♨️ Thermal Modeling
- Thermal model creation & parametrization
- S1/S3, Rated & Peak curves
- In-depth thermal simulations & analysis
🧠 Intelligent Derating Functions
- Rotor & Stator Temperature Derating
- Inverter Coolant Temperature Derating
- HV AC/DC Current (I²t) Derating
- IGBT Temperature Delta Derating
- Inverter PWM Frequency & NTC Temp Derating
📉 Detailed Loss Modeling for Peak Drivetrain Efficiency
- Electric motor loss determination
- Friction, proximity, skin effect, iron & magnet loss analysis
- Thermal efficiency maps under varied conditions
- Software parametrization, curve fitting & optimization
✅ Validation & Verification
- Rigorous Testing & Validation According to Global Standards
- Test bench support: Sample A/B/C/D, prototype, and type testing
- Creation of Design Validation Plans
- Compliance for ISO26262, DO160, DO178c, IEC 60034-18
Powering Every Industry: Scalable Voltage, Versatile Applications
- 🔌 DC Voltage Levels:
- ⚡ Power Ranges:
- 🚗 Applications Covered:
- 12–48V: conventional systems
- 48V: hybrid & low power
- 400V: traction drives, industrial machinery
- 800V: eBus, eTruck, mining
- 1200V–2400V: aerospace
- 5–25kW: starter/generator/mild hybrid
- 100–300kW: electric/hybrid vehicles
- 150–600kW: eBus, eTruck, mining
- 650–1000kW: racing, aerospace
- 10MW: wind power, energy applications
- BEV, EREV, PHEV, HEV
- Electric Busses & Trucks (traction, axial drive)
- Heavy-duty trucks & machinery
- eVTOL, hybrid electric aviation
- Mining & industrial applications
Proven Electric Drivetrain Modeling and Simulation Excellence
Drivetrain Development That Meets Industry Standards:
- ISO26262
- DO160
- DO178c
- IEC 60034-18
Agile & Certified Engineering Processes That Drive Results:
- ASPICE
- V-Model
- Kaizen & Lean
- Six Sigma
- Agile, Scrum, Kanban Processes, Sprint Planning
Interdisciplinary Mechanical, System-Level and Project Management Support:
- CAD design, drawing creation of motor components
- System-level modeling & simulation
- Mechanical integration into overall system
- Stress analysis: CAD engineering, FEM calculations
- Project management, product owner, scrum master support
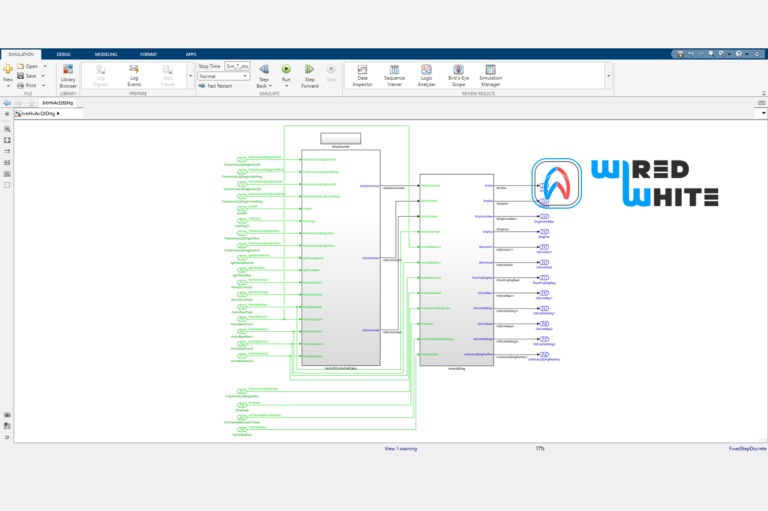
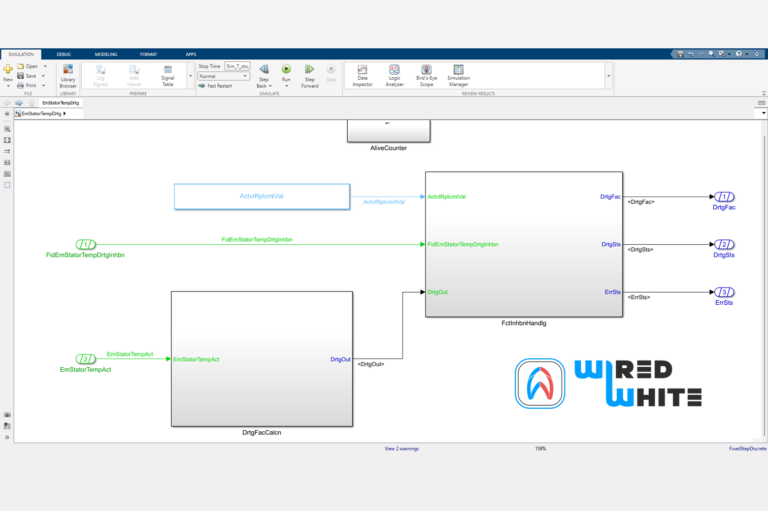
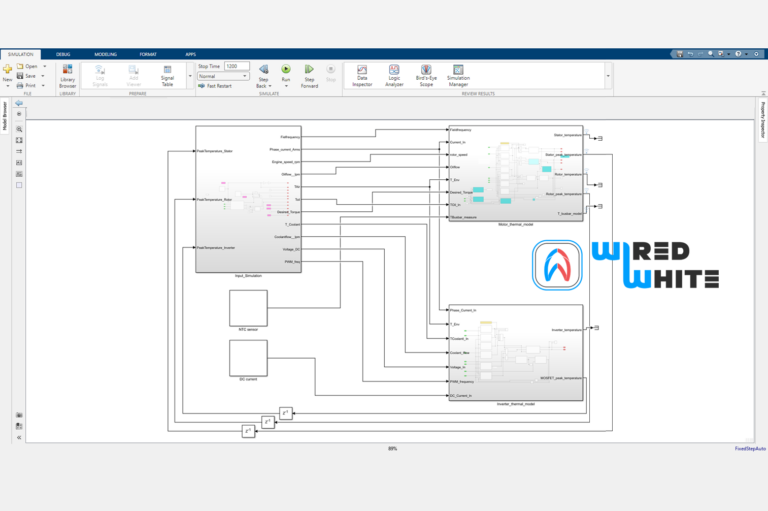
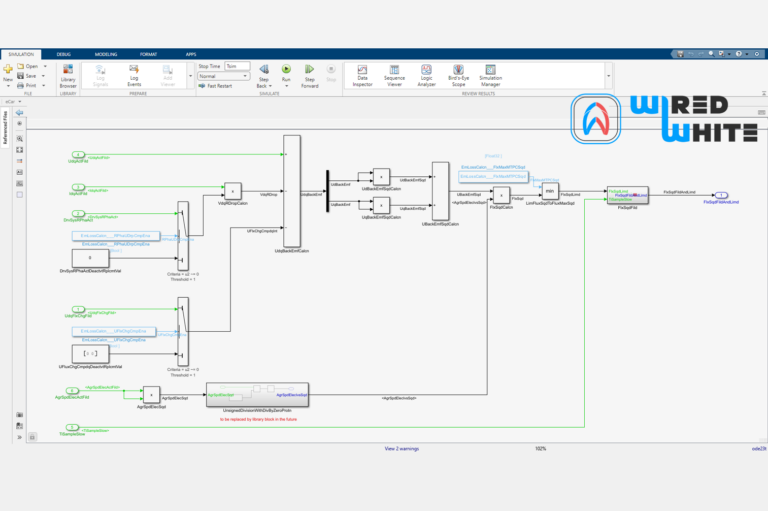
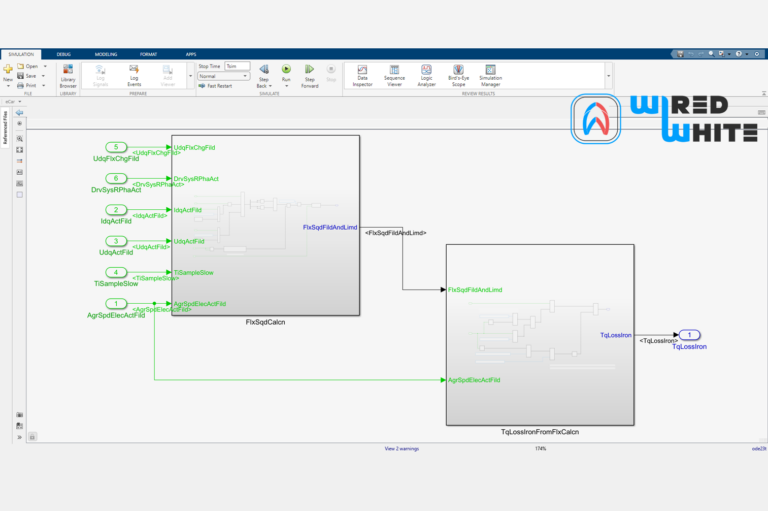
Advanced Engineering Tools and Collaboration Platform for Electric Drivetrain Modeling & Simulation
Our powerful tech stack enables fast, precise, and collaborative engineering workflows:
Specialized Simulation Software for Electric Motors
- Ansys Maxwell 2D – FEM-based electromagnetic simulations
- Motor-CAD – Thermal and electromagnetic analysis for e-motor systems
- MATLAB & Simulink – Model-based development, control algorithms, and system simulation
- CANape, INCA, TargetLink, dSPACE, LabVIEW – ECU calibration, testing, code generation, and real-time validation
Integrated Collaboration Tools: WiredWhite Platform
- Project-specific workspaces for seamless teamwork
- Kanban boards and task management
- Video conferencing with screen sharing and recording
- Structured document handling and other useful tools
Supporting Standard Software
- Microsoft 365 – Teams, Word, Excel, PowerPoint for communication and documentation
Why WiredWhite is the Perfect Engineering Partner for You
⏱ 15+ Years
industry experience
👨 800+
networked engineering professionals
🔄 Integrated
project collaboration tools
✅ 100%
Proficient in advanced engineering tools
We Are Supporting Businesses, Executives, and Innovators Worldwide
Freelance Agencies
Teams of Engineers
Start-ups
Companies
Motor Solutions for Every Business
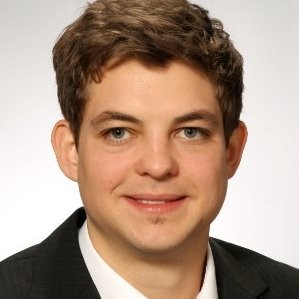
Sara, Account-ManagerinSOLCOM GmbH
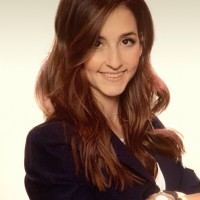
Katharina, Team Lead Rolling Stockemagine GmbH
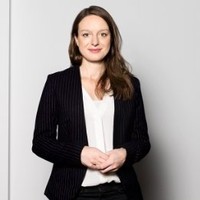
Martin, Domain Lead Electrical SystemsALSTOM Drives GmbH
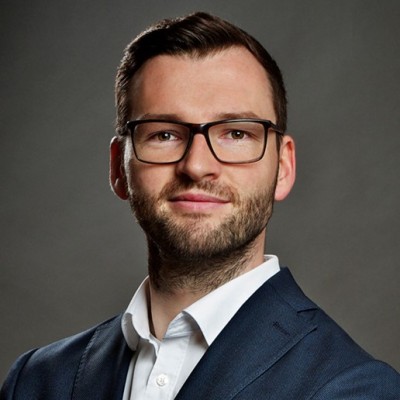
Stefanie, Service Delivery Managerinemagine GmbH
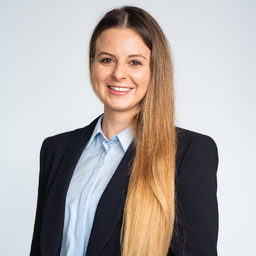
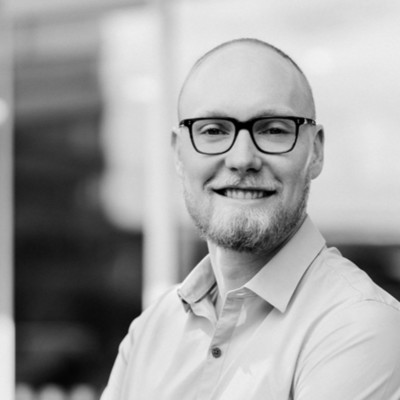
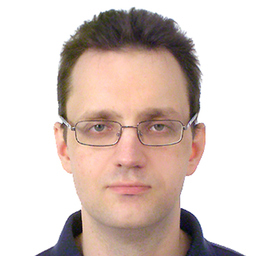
Theresa, Proficient Key Account ManagerSOLCOM GmbH
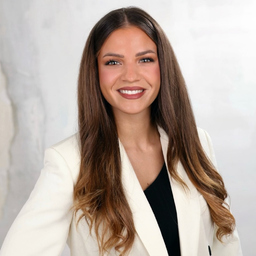
Max, Technical Project Lead E-DrivesNidec Motors & Actuators (Germany) GmbH
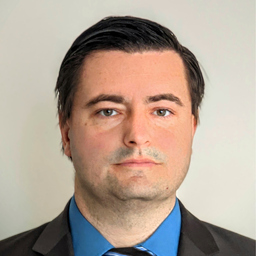
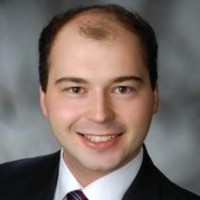
Franziska, Principal ConsultantAmoria Bond GmbH
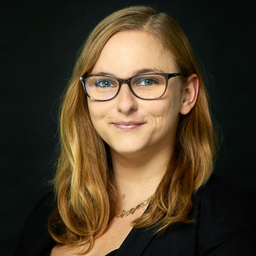
Seán, Chief Executive OfficerGrip Factory Munich GmbH
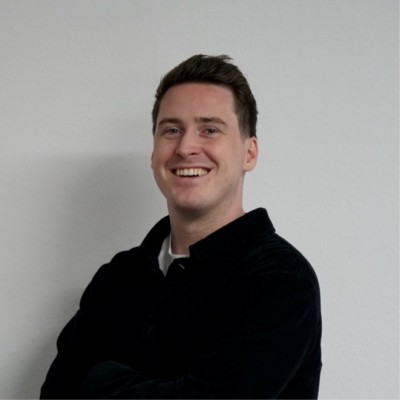
- Free consultation call
- Contact form
Partner with Us for Your Electric Drivetrain Modeling & Simulation Project
Speak directly with our drivetrain experts to explore how we can help you model, simulate, and validate electric propulsion systems — with speed, precision, and full standards compliance.
Let’s move your ideas forward.