Standstill Frequency Response Test for Obtaining Parameters of Six Phase Double Delta Salient-Pole Synchronous Machine on Example of Claw-Pole Alternator
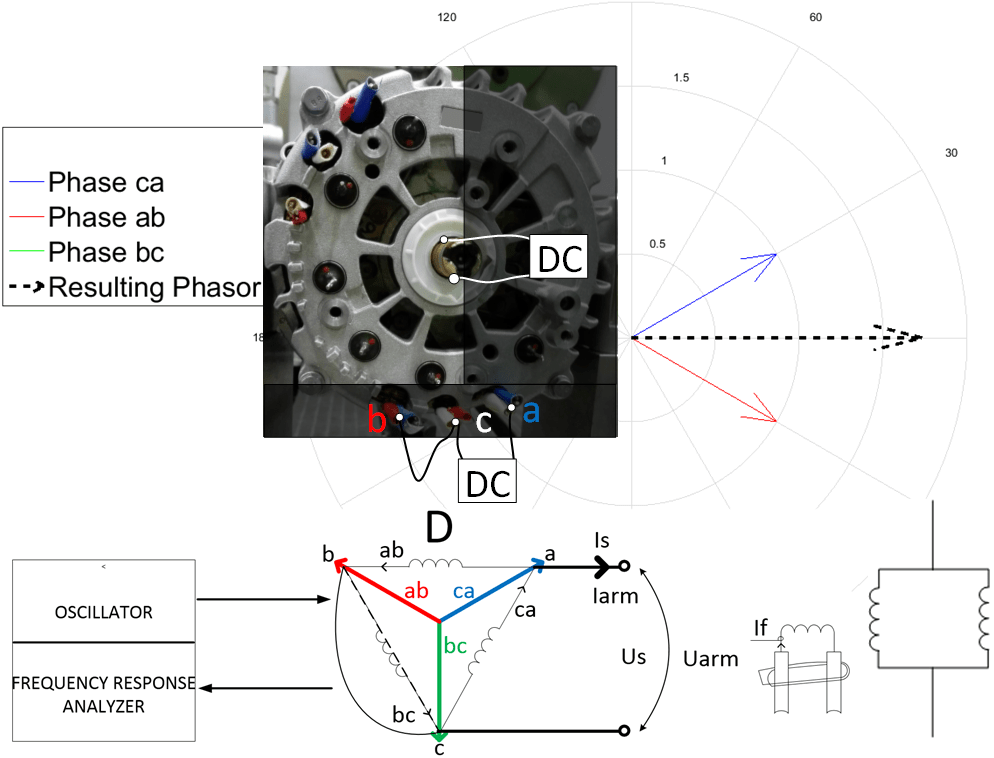
The current publication introduces an approach for obtaining parameters of a six phase double delta salient-pole synchronous machine, based on the standstill frequency response test. The described approach was verified by measurements on a automotive claw-pole alternator, done in a laboratory on a test bench.